Destylarka do rozpuszczalnika to urządzenie, które wykorzystuje proces destylacji do oddzielania różnych składników chemicznych na podstawie ich temperatury wrzenia. W praktyce oznacza to, że substancje o niższej temperaturze wrzenia będą parować jako pierwsze, a następnie skraplać się w chłodnicy, co pozwala na ich zbieranie w osobnym pojemniku. Proces ten jest niezwykle przydatny w laboratoriach chemicznych oraz w przemyśle, gdzie czystość rozpuszczalników ma kluczowe znaczenie dla jakości końcowego produktu. Destylacja może być przeprowadzana w różnych warunkach, takich jak podciśnienie, co obniża temperaturę wrzenia i pozwala na destylację substancji wrażliwych na wysoką temperaturę. Warto również zauważyć, że destylarki mogą być używane do odzyskiwania rozpuszczalników, co jest korzystne zarówno z ekonomicznego, jak i ekologicznego punktu widzenia.
Jakie są najlepsze materiały do budowy destylarki
Wybór odpowiednich materiałów do budowy destylarki do rozpuszczalnika ma kluczowe znaczenie dla jej efektywności oraz bezpieczeństwa użytkowania. Najczęściej wykorzystywanym materiałem jest stal nierdzewna, która charakteryzuje się wysoką odpornością na korozję oraz łatwością w utrzymaniu czystości. Innym popularnym wyborem jest szkło borokrzemowe, które jest odporne na wysokie temperatury i chemikalia, co czyni je idealnym materiałem dla elementów kontaktujących się z destylowanymi substancjami. W przypadku chłodnic często stosuje się miedź ze względu na jej doskonałe właściwości przewodzenia ciepła. Ważne jest również, aby wszystkie uszczelki były wykonane z materiałów odpornych na działanie chemikaliów, aby uniknąć niepożądanych reakcji. Warto również zwrócić uwagę na jakość połączeń i spoin, ponieważ nieszczelności mogą prowadzić do utraty cennych substancji oraz stwarzać zagrożenie dla zdrowia użytkowników.
Jakie zastosowania ma destylarka do rozpuszczalnika
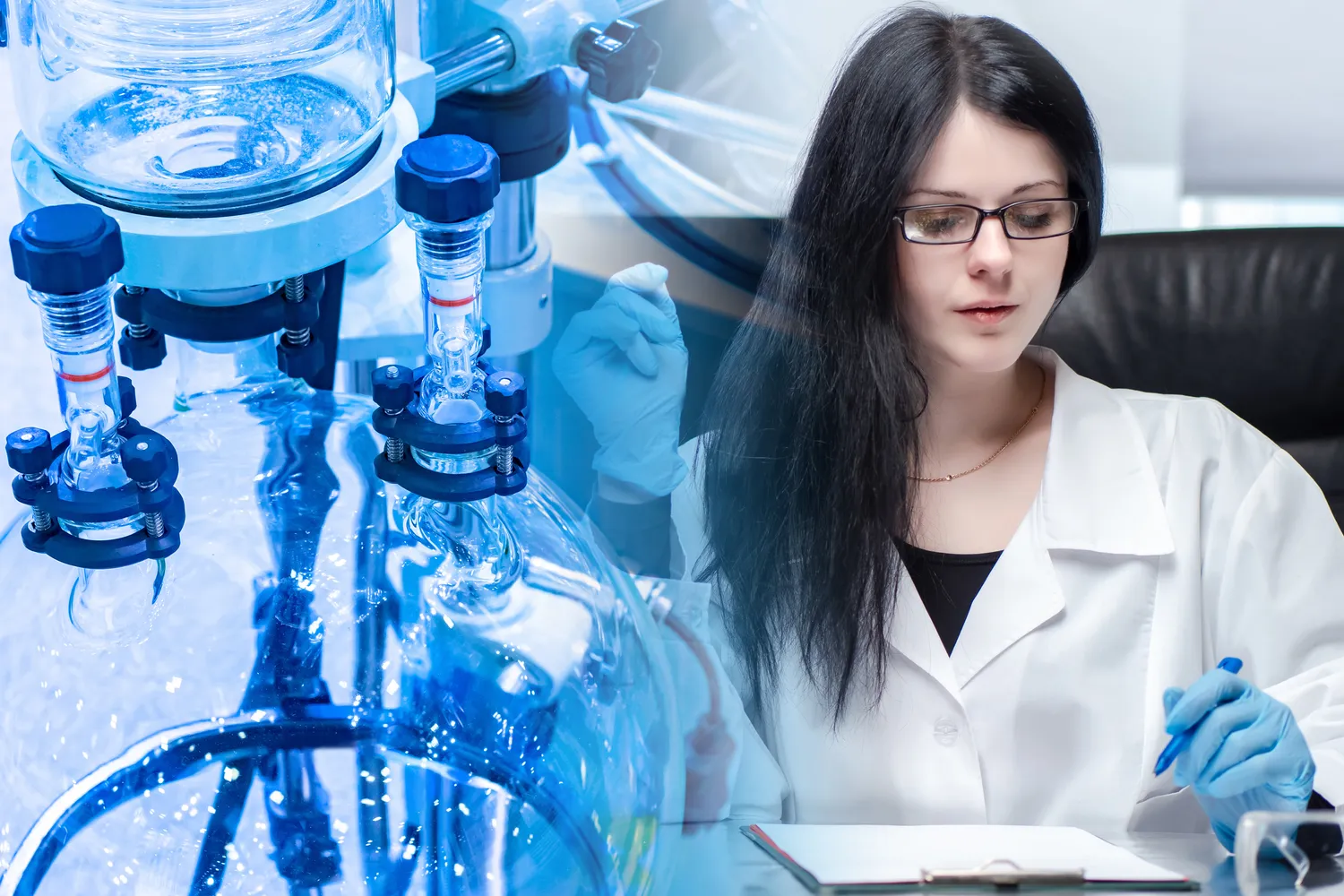
Destylarka do rozpuszczalnika
Destylarka do rozpuszczalnika znajduje szerokie zastosowanie w różnych dziedzinach przemysłu oraz nauki. W laboratoriach chemicznych jest niezbędna do oczyszczania substancji chemicznych oraz przygotowywania roztworów o określonej czystości. Dzięki możliwości separacji składników można uzyskać wysokiej jakości reagenty, które są kluczowe w badaniach naukowych. W przemyśle farmaceutycznym destylarki są wykorzystywane do produkcji leków oraz ekstraktów roślinnych, gdzie czystość składników ma ogromne znaczenie dla skuteczności terapeutycznej. Ponadto w przemyśle kosmetycznym destylacja pozwala na pozyskiwanie olejków eterycznych oraz innych substancji aktywnych stosowanych w produktach pielęgnacyjnych. W sektorze spożywczym destylarki są używane do produkcji alkoholi oraz aromatów, co wpływa na jakość finalnych produktów. Również w branży petrochemicznej proces destylacji jest kluczowy dla separacji różnych frakcji ropy naftowej, co pozwala na uzyskanie paliw oraz innych produktów chemicznych.
Jakie są najważniejsze cechy dobrej destylarki
Wybór odpowiedniej destylarki do rozpuszczalnika powinien opierać się na kilku kluczowych cechach, które wpływają na jej wydajność i bezpieczeństwo użytkowania. Przede wszystkim istotna jest pojemność urządzenia, która powinna być dostosowana do potrzeb użytkownika oraz skali produkcji. Dobrze zaprojektowana destylarka powinna mieć efektywny system chłodzenia, który zapewnia szybkie skraplanie pary i minimalizuje straty materiału. Ważnym aspektem jest także łatwość obsługi i konserwacji urządzenia; im prostsza konstrukcja, tym mniej problemów podczas eksploatacji. Kolejną istotną cechą jest możliwość regulacji temperatury i ciśnienia, co pozwala na dostosowanie procesu destylacji do specyfiki używanych substancji. Bezpieczeństwo użytkownika to kolejny ważny element; dobra destylarka powinna być wyposażona w systemy zabezpieczające przed przegrzaniem czy wyciekiem szkodliwych substancji.
Jakie są najczęstsze problemy z destylarką do rozpuszczalnika
Podczas użytkowania destylarki do rozpuszczalnika mogą wystąpić różne problemy, które mogą wpływać na efektywność procesu oraz bezpieczeństwo pracy. Jednym z najczęstszych problemów jest nieszczelność, która może prowadzić do utraty cennych substancji oraz stwarzać zagrożenie dla zdrowia użytkowników. Nieszczelności mogą występować w miejscach połączeń elementów, uszczelek czy zaworów, dlatego regularne kontrole i konserwacja są kluczowe dla zapewnienia prawidłowego działania urządzenia. Innym powszechnym problemem jest zatykanie się chłodnicy, co może prowadzić do obniżenia efektywności skraplania pary. Zatkanie może być spowodowane osadami chemicznymi lub zanieczyszczeniami, dlatego ważne jest, aby dbać o czystość wszystkich elementów. W przypadku nieodpowiednich ustawień temperatury lub ciśnienia może dojść do niepełnej destylacji, co skutkuje uzyskaniem nieczystych produktów. Użytkownicy powinni być świadomi właściwych parametrów pracy dla używanych substancji oraz regularnie monitorować proces destylacji. Warto również zwrócić uwagę na ryzyko przegrzania urządzenia, co może prowadzić do uszkodzeń oraz zwiększonego ryzyka pożaru.
Jakie są koszty zakupu i eksploatacji destylarki
Koszty zakupu destylarki do rozpuszczalnika mogą się znacznie różnić w zależności od jej wielkości, materiałów użytych do produkcji oraz dodatkowych funkcji. Proste modele laboratoryjne można nabyć już za kilka tysięcy złotych, podczas gdy bardziej zaawansowane urządzenia przemysłowe mogą kosztować nawet kilkadziesiąt tysięcy złotych. Warto jednak pamiętać, że cena zakupu to tylko część całkowitych kosztów związanych z eksploatacją destylarki. Użytkownicy muszą także uwzględnić koszty energii elektrycznej potrzebnej do ogrzewania oraz chłodzenia, a także koszty konserwacji i ewentualnych napraw. Regularne przeglądy techniczne są kluczowe dla zapewnienia długotrwałej i bezawaryjnej pracy urządzenia. Dodatkowo należy brać pod uwagę koszty związane z zakupem rozpuszczalników oraz innych materiałów eksploatacyjnych, które mogą być potrzebne w trakcie procesu destylacji. W przypadku dużych zakładów przemysłowych warto rozważyć inwestycję w systemy odzysku rozpuszczalników, które mogą znacząco obniżyć koszty operacyjne poprzez ponowne wykorzystanie materiałów.
Jakie są różnice między różnymi typami destylarek
Na rynku dostępnych jest wiele różnych typów destylarek do rozpuszczalników, które różnią się konstrukcją, przeznaczeniem oraz metodą działania. Najpopularniejsze typy to destylarki proste, frakcyjne oraz rotacyjne. Destylarka prosta jest najczęściej stosowana w laboratoriach do podstawowych procesów oczyszczania substancji chemicznych; jej działanie opiera się na jednorazowej separacji składników na podstawie ich temperatury wrzenia. Destylarka frakcyjna jest bardziej zaawansowana i pozwala na oddzielanie wielu składników jednocześnie dzięki zastosowaniu kolumny frakcyjnej, co czyni ją idealną do bardziej skomplikowanych procesów przemysłowych. Rotacyjne destylatory natomiast charakteryzują się obrotowym zbiornikiem, co umożliwia efektywne odparowywanie substancji przy niższej temperaturze; są szczególnie przydatne w przypadku delikatnych substancji chemicznych lub tych wrażliwych na wysoką temperaturę. Każdy z tych typów ma swoje zalety i ograniczenia, dlatego wybór odpowiedniej destylarki powinien być dostosowany do specyfiki procesu oraz rodzaju używanych substancji.
Jakie są zasady bezpieczeństwa przy używaniu destylarki
Bezpieczeństwo podczas pracy z destylarką do rozpuszczalnika jest kluczowe ze względu na potencjalne zagrożenia związane z używanymi substancjami chemicznymi oraz wysokimi temperaturami. Przede wszystkim użytkownicy powinni zawsze nosić odpowiednią odzież ochronną, taką jak rękawice, gogle i fartuchy laboratoryjne, aby zminimalizować ryzyko kontaktu z niebezpiecznymi substancjami. Ważne jest również zapewnienie odpowiedniej wentylacji w pomieszczeniu, w którym znajduje się destylarka; wiele rozpuszczalników jest łatwopalnych lub toksycznych, dlatego unikanie gromadzenia się oparów jest kluczowe dla bezpieczeństwa. Użytkownicy powinni także zapoznać się z kartami charakterystyki używanych substancji chemicznych oraz stosować się do zaleceń dotyczących ich przechowywania i obsługi. Regularne przeglądy techniczne urządzenia są niezbędne dla zapewnienia jego sprawności; wszelkie uszkodzenia powinny być natychmiast naprawiane przez wykwalifikowany personel. Warto również mieć pod ręką gaśnicę odpowiednią do gaszenia pożarów chemicznych oraz zestaw pierwszej pomocy na wypadek nagłych sytuacji.
Jakie innowacje technologiczne wpływają na rozwój destylarek
W ostatnich latach obserwuje się dynamiczny rozwój technologii związanych z produkcją i użytkowaniem destylarek do rozpuszczalników. Innowacje te mają na celu poprawę efektywności procesów destylacyjnych oraz zwiększenie bezpieczeństwa użytkowników. Jednym z najważniejszych trendów jest automatyzacja procesów; nowoczesne destylarki często wyposażone są w zaawansowane systemy sterowania, które umożliwiają precyzyjne monitorowanie temperatury i ciśnienia w czasie rzeczywistym. Dzięki temu możliwe jest osiągnięcie optymalnych warunków pracy bez konieczności ciągłego nadzoru ze strony operatora. Kolejnym istotnym kierunkiem rozwoju jest zastosowanie materiałów kompozytowych i nanotechnologii w budowie elementów destylarek; materiały te charakteryzują się lepszymi właściwościami termicznymi oraz odpornością na korozję. Wprowadzenie systemów odzysku energii pozwala również na zmniejszenie kosztów operacyjnych poprzez ponowne wykorzystanie ciepła generowanego podczas procesu destylacji. Dodatkowo rozwijają się technologie związane z ekologicznymi rozwiązaniami; wiele nowoczesnych urządzeń projektowanych jest z myślą o minimalizacji wpływu na środowisko poprzez redukcję emisji szkodliwych substancji czy zużycia energii.
Jak wybrać odpowiednią destylarkę do swoich potrzeb
Wybór odpowiedniej destylarki do rozpuszczalnika powinien być dokładnie przemyślany i dostosowany do specyfiki planowanych zastosowań oraz rodzaju używanych substancji chemicznych. Pierwszym krokiem jest określenie wymagań dotyczących pojemności urządzenia; warto zastanowić się nad ilością materiału, którą zamierza się przetwarzać w danym czasie oraz częstotliwością użytkowania sprzętu. Następnie należy zwrócić uwagę na typ destylarki; wybór między modelem prostym a frakcyjnym zależy od stopnia skomplikowania procesu oczyszczania oraz wymaganej czystości końcowego produktu. Kolejnym istotnym aspektem są materiały wykonania; stal nierdzewna czy szkło borokrzemowe to najlepsze opcje ze względu na ich odporność na działanie chemikaliów i wysokich temperatur.