Destylacja rozpuszczalników to proces, który polega na oddzieleniu substancji na podstawie różnicy w ich temperaturach wrzenia. W praktyce oznacza to, że ciecz o niższej temperaturze wrzenia odparowuje jako pierwsza, a następnie skrapla się w chłodnicy, tworząc czystszy produkt. Proces ten jest szeroko stosowany w chemii oraz przemyśle, gdzie konieczne jest uzyskanie wysokiej czystości rozpuszczalników. Aby przeprowadzić destylację, niezbędne jest posiadanie odpowiedniego sprzętu, takiego jak kolumna destylacyjna, balon destylacyjny oraz chłodnica. Ważnym aspektem jest również kontrola temperatury, która musi być precyzyjna, aby zapewnić efektywność procesu. Warto również zwrócić uwagę na właściwości fizyczne rozpuszczalników, takie jak ich gęstość czy lepkość, które mogą wpływać na przebieg destylacji. Różne metody destylacji, takie jak destylacja prosta czy frakcyjna, mogą być stosowane w zależności od rodzaju substancji i pożądanego efektu końcowego.
Jakie są zastosowania destylacji rozpuszczalników w przemyśle
Destylacja rozpuszczalników znajduje szerokie zastosowanie w różnych gałęziach przemysłu, co czyni ją niezwykle istotnym procesem technologicznym. W przemyśle chemicznym wykorzystywana jest do oczyszczania surowców oraz produkcji wysokiej jakości substancji chemicznych. Na przykład w produkcji alkoholi etylowych destylacja pozwala na uzyskanie czystego spirytusu poprzez usunięcie zanieczyszczeń i innych składników o wyższej temperaturze wrzenia. W przemyśle farmaceutycznym proces ten jest kluczowy dla produkcji leków, gdzie czystość substancji czynnych ma ogromne znaczenie dla bezpieczeństwa pacjentów. Ponadto destylacja rozpuszczalników ma zastosowanie w przemyśle petrochemicznym, gdzie służy do separacji różnych frakcji ropy naftowej. Dzięki temu możliwe jest uzyskanie paliw oraz innych produktów chemicznych o określonych właściwościach. Warto również zauważyć, że destylacja jest wykorzystywana w laboratoriach badawczych do analizy i oczyszczania substancji chemicznych, co przyczynia się do postępu naukowego i technologicznego.
Jakie są różnice między destylacją prostą a frakcyjną
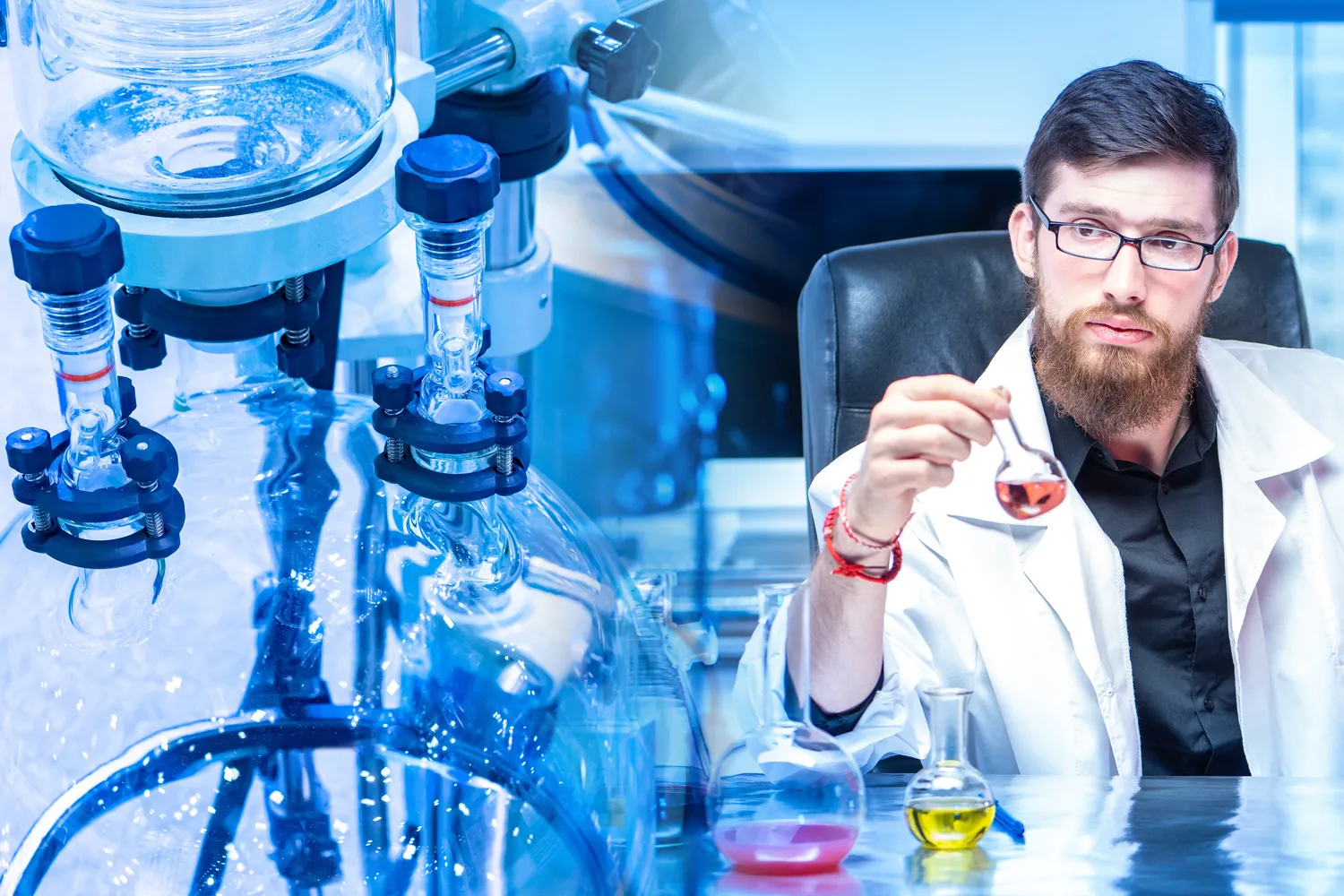
Destylacja rozpuszczalników
W kontekście destylacji rozpuszczalników istnieją dwie główne metody: destylacja prosta i frakcyjna, które różnią się zarówno pod względem techniki wykonania, jak i zastosowania. Destylacja prosta jest najprostszą formą tego procesu i polega na odparowaniu cieczy oraz jej skropleniu bez użycia dodatkowych elementów separacyjnych. Jest ona skuteczna jedynie w przypadku substancji o znacznej różnicy temperatur wrzenia oraz niskiej liczbie składników. Z kolei destylacja frakcyjna wykorzystuje kolumny destylacyjne z wieloma poziomami separacyjnymi, co pozwala na bardziej efektywne oddzielanie składników o zbliżonych temperaturach wrzenia. Dzięki temu metoda ta jest idealna do oczyszczania mieszanin wieloskładnikowych oraz uzyskiwania wysokiej czystości produktów końcowych. W praktyce wybór metody zależy od specyfiki danej aplikacji oraz wymagań dotyczących czystości końcowego produktu.
Jakie są najważniejsze etapy procesu destylacji rozpuszczalników
Proces destylacji rozpuszczalników składa się z kilku kluczowych etapów, które są niezbędne do osiągnięcia pożądanego efektu końcowego. Pierwszym krokiem jest przygotowanie surowca, który ma zostać poddany destylacji. Należy upewnić się, że substancja jest odpowiednio oczyszczona i nie zawiera zanieczyszczeń mogących wpłynąć na wyniki procesu. Następnie surowiec umieszczany jest w balonie destylacyjnym i podgrzewany do momentu osiągnięcia temperatury wrzenia cieczy o niższej temperaturze wrzenia. Gdy ciecz zaczyna parować, powstaje para wodna, która przemieszcza się do chłodnicy, gdzie następuje jej skroplenie. Skroplony produkt zbierany jest w osobnym naczyniu jako produkt końcowy. W przypadku destylacji frakcyjnej proces ten obejmuje dodatkowe etapy związane z wieloma cyklami parowania i skraplania wewnątrz kolumny destylacyjnej. Ostatnim etapem jest analiza jakości uzyskanego produktu oraz ewentualne dalsze oczyszczanie lub modyfikacje chemiczne w celu uzyskania pożądanych właściwości końcowych.
Jakie są najczęstsze błędy podczas destylacji rozpuszczalników
Podczas przeprowadzania destylacji rozpuszczalników, zarówno w warunkach laboratoryjnych, jak i przemysłowych, mogą wystąpić różne błędy, które wpływają na efektywność procesu oraz jakość uzyskanego produktu. Jednym z najczęstszych błędów jest niewłaściwe ustawienie temperatury. Zbyt wysoka temperatura może prowadzić do niekontrolowanego odparowania substancji, co skutkuje utratą cennych składników oraz zanieczyszczeniem produktu końcowego. Z kolei zbyt niska temperatura może spowodować, że proces destylacji będzie nieefektywny, a uzyskany produkt nie osiągnie wymaganej czystości. Innym powszechnym problemem jest niewłaściwe dobranie sprzętu, co może prowadzić do nieoptymalnych warunków pracy. Na przykład użycie kolumny destylacyjnej o niewłaściwej wysokości lub liczbie poziomów separacyjnych może wpłynąć na skuteczność oddzielania składników. Dodatkowo, brak odpowiedniej kontroli nad ciśnieniem w systemie może prowadzić do nieprzewidywalnych rezultatów. Ważne jest również monitorowanie jakości surowca przed rozpoczęciem procesu, ponieważ obecność zanieczyszczeń może znacząco wpłynąć na wyniki destylacji.
Jakie czynniki wpływają na efektywność destylacji rozpuszczalników
Efektywność procesu destylacji rozpuszczalników zależy od wielu czynników, które mogą znacząco wpłynąć na wyniki końcowe. Jednym z najważniejszych aspektów jest różnica temperatur wrzenia poszczególnych składników mieszaniny. Im większa różnica, tym łatwiejsze jest oddzielenie substancji. W przypadku substancji o zbliżonych temperaturach wrzenia, proces staje się bardziej skomplikowany i wymaga zastosowania bardziej zaawansowanych technik, takich jak destylacja frakcyjna. Kolejnym istotnym czynnikiem jest ciśnienie atmosferyczne, które wpływa na temperatury wrzenia cieczy. W obniżonym ciśnieniu substancje mogą wrzeć w niższych temperaturach, co może być korzystne w przypadku delikatnych związków chemicznych, które mogłyby ulec degradacji w wyższych temperaturach. Również czas trwania procesu ma znaczenie; zbyt krótki czas może skutkować niedostatecznym oczyszczeniem, podczas gdy zbyt długi czas może prowadzić do utraty cennych składników.
Jakie są nowoczesne technologie stosowane w destylacji rozpuszczalników
W ostatnich latach nastąpił znaczny rozwój technologii związanych z destylacją rozpuszczalników, co przyczyniło się do zwiększenia efektywności oraz jakości tego procesu. Nowoczesne systemy destylacyjne często wykorzystują automatyzację i zaawansowane technologie monitorowania, co pozwala na precyzyjne kontrolowanie parametrów procesu, takich jak temperatura czy ciśnienie. Przykładem innowacyjnej technologii jest zastosowanie membran w procesach separacyjnych, które umożliwiają selektywne oddzielanie składników bez konieczności ich odparowywania. Membrany te mogą być wykorzystywane w połączeniu z tradycyjnymi metodami destylacyjnymi, co zwiększa efektywność całego procesu oraz zmniejsza zużycie energii. Ponadto rozwój nanotechnologii przyczynił się do powstania nowych materiałów o wysokiej wydajności do budowy kolumn destylacyjnych, co pozwala na lepsze separowanie składników o podobnych właściwościach fizycznych. Warto również wspomnieć o zastosowaniu technologii komputerowych do symulacji procesów destylacyjnych, co pozwala na optymalizację warunków pracy jeszcze przed rozpoczęciem rzeczywistego procesu.
Jakie są ekologiczne aspekty związane z destylacją rozpuszczalników
Destylacja rozpuszczalników wiąże się nie tylko z korzyściami technologicznymi i ekonomicznymi, ale także z kwestiami ekologicznymi, które stają się coraz bardziej istotne w kontekście ochrony środowiska. Proces ten często wymaga dużych ilości energii do podgrzewania cieczy oraz chłodzenia pary, co może prowadzić do znacznego zużycia zasobów energetycznych i emisji gazów cieplarnianych. Dlatego ważne jest poszukiwanie alternatywnych metod redukcji zużycia energii oraz zastosowanie odnawialnych źródeł energii w procesach przemysłowych. W ostatnich latach pojawiły się także technologie umożliwiające recykling rozpuszczalników po ich użyciu, co pozwala na zmniejszenie ilości odpadów chemicznych oraz obniżenie kosztów zakupu nowych surowców. Dodatkowo rozwój bardziej ekologicznych substancji chemicznych jako alternatywy dla tradycyjnych rozpuszczalników przyczynia się do zmniejszenia negatywnego wpływu na środowisko naturalne. Warto również zwrócić uwagę na regulacje prawne dotyczące emisji substancji szkodliwych oraz normy dotyczące bezpieczeństwa chemicznego, które nakładają obowiązki na przedsiębiorstwa zajmujące się destylacją rozpuszczalników.
Jakie są przyszłe kierunki rozwoju technologii destylacji rozpuszczalników
Przyszłość technologii destylacji rozpuszczalników zapowiada się obiecująco dzięki ciągłemu postępowi naukowemu oraz innowacjom technologicznym. W miarę jak rośnie zapotrzebowanie na wysokiej jakości produkty chemiczne oraz ekologiczne rozwiązania, badania nad nowymi metodami separacyjnymi stają się coraz bardziej intensywne. Jednym z kierunków rozwoju jest integracja procesów chemicznych z technologią informacyjną i sztuczną inteligencją, co pozwoli na lepsze modelowanie i optymalizację procesów produkcyjnych. Dzięki temu możliwe będzie przewidywanie wyników eksperymentów i dostosowywanie parametrów pracy w czasie rzeczywistym. Ponadto rozwój materiałów nanostrukturalnych otwiera nowe możliwości dla konstrukcji kolumn destylacyjnych o wyższej wydajności i mniejszym zużyciu energii. Wzrost zainteresowania biotechnologią również przyczynia się do poszukiwania naturalnych i odnawialnych źródeł surowców chemicznych, co może wpłynąć na sposób przeprowadzania procesów destylacyjnych. Równocześnie rosnąca świadomość ekologiczna społeczeństwa wymusza zmiany w przemyśle chemicznym w kierunku bardziej zrównoważonego rozwoju i minimalizacji wpływu działalności przemysłowej na środowisko naturalne.