Destylator przemysłowy to urządzenie, które służy do oddzielania składników cieczy na podstawie różnic w ich temperaturach wrzenia. Proces ten jest kluczowy w wielu branżach, takich jak przemysł chemiczny, petrochemiczny czy spożywczy. W destylacji wykorzystuje się zjawisko parowania, gdzie ciecz podgrzewana do określonej temperatury przechodzi w stan gazowy, a następnie skrapla się w chłodnicy, co pozwala na uzyskanie czystego produktu. W przemyśle chemicznym destylatory są wykorzystywane do oczyszczania substancji chemicznych oraz separacji różnych frakcji. W przemyśle petrochemicznym proces ten jest niezbędny do uzyskiwania paliw oraz innych produktów naftowych. W branży spożywczej destylatory są stosowane do produkcji alkoholu, olejków eterycznych oraz aromatów.
Jakie są rodzaje destylatorów przemysłowych i ich różnice
Wśród różnych rodzajów destylatorów przemysłowych można wyróżnić kilka podstawowych typów, które różnią się konstrukcją oraz zastosowaniem. Najpopularniejsze z nich to destylatory prostokątne, kolumnowe oraz próżniowe. Destylatory prostokątne charakteryzują się prostą budową i są często wykorzystywane w mniejszych zakładach produkcyjnych. Ich zaletą jest łatwość obsługi oraz niskie koszty eksploatacji. Z kolei destylatory kolumnowe są bardziej zaawansowane technologicznie i umożliwiają prowadzenie procesów na większą skalę. Dzięki zastosowaniu kolumny frakcyjnej możliwe jest uzyskanie wyższej czystości produktów oraz lepsza separacja składników. Destylatory próżniowe natomiast działają w obniżonym ciśnieniu, co pozwala na destylację substancji w niższych temperaturach, co jest szczególnie istotne dla termolabilnych związków chemicznych.
Jakie są kluczowe elementy konstrukcyjne destylatora przemysłowego
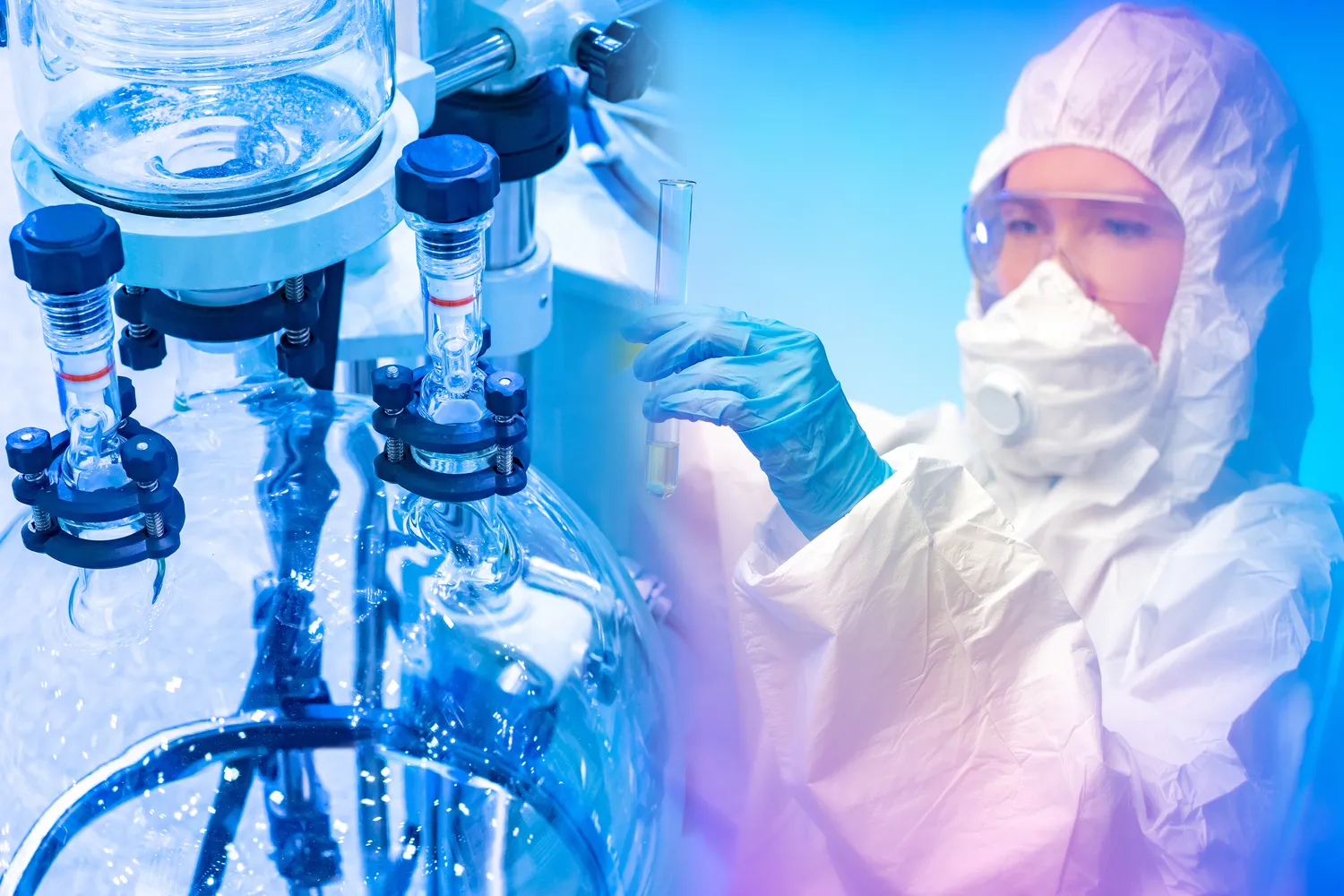
Destylator przemysłowy
Kluczowe elementy konstrukcyjne destylatora przemysłowego obejmują kilka istotnych komponentów, które współpracują ze sobą w celu zapewnienia efektywności procesu destylacji. Podstawowym elementem jest zbiornik do podgrzewania cieczy, który może być wyposażony w różne źródła ciepła, takie jak palniki gazowe czy grzałki elektryczne. Kolejnym ważnym elementem jest kolumna frakcyjna, która umożliwia separację składników na podstawie różnic w temperaturze wrzenia. W górnej części kolumny znajduje się chłodnica, która skrapla parę i zbiera gotowy produkt. Dodatkowo wiele nowoczesnych destylatorów wyposażonych jest w systemy automatyzacji, które monitorują i kontrolują parametry procesu, takie jak temperatura czy ciśnienie. Inne istotne komponenty to pompy transportowe oraz systemy filtracyjne, które zapewniają odpowiednią jakość surowców oraz gotowych produktów.
Jakie są korzyści z użycia nowoczesnych destylatorów przemysłowych
Nowoczesne destylatory przemysłowe oferują szereg korzyści, które przyczyniają się do zwiększenia efektywności produkcji oraz poprawy jakości finalnych produktów. Jedną z głównych zalet jest możliwość automatyzacji procesów, co pozwala na minimalizację błędów ludzkich oraz zwiększenie precyzji operacji. Dzięki zastosowaniu zaawansowanych technologii monitorowania i kontroli parametrów procesowych możliwe jest osiągnięcie optymalnych warunków pracy urządzenia, co przekłada się na wyższą wydajność i mniejsze straty surowców. Nowoczesne destylatory są również bardziej energooszczędne niż ich starsze odpowiedniki, co wpływa na obniżenie kosztów eksploatacji. Dodatkowo wiele z nich jest zaprojektowanych z myślą o ochronie środowiska, co oznacza mniejsze emisje szkodliwych substancji oraz lepsze zarządzanie odpadami.
Jakie są najczęstsze problemy z destylatorami przemysłowymi
Destylatory przemysłowe, mimo swojej zaawansowanej technologii, mogą napotykać różne problemy, które wpływają na ich wydajność i jakość produkcji. Jednym z najczęściej występujących problemów jest osadzanie się zanieczyszczeń w kolumnach frakcyjnych, co prowadzi do obniżenia efektywności separacji składników. Osady te mogą pochodzić z surowców używanych w procesie destylacji lub być wynikiem reakcji chemicznych zachodzących w trakcie procesu. Innym istotnym problemem jest niewłaściwe ustawienie parametrów pracy urządzenia, takich jak temperatura czy ciśnienie, co może prowadzić do niepełnej destylacji lub uzyskania produktów o niskiej czystości. Problemy z systemami chłodzenia również mogą wpływać na wydajność destylacji, ponieważ niewłaściwe skraplanie pary może prowadzić do strat produktu. Warto również zwrócić uwagę na kwestie związane z konserwacją i regularnym serwisowaniem urządzeń, ponieważ zaniedbania w tym zakresie mogą prowadzić do poważnych awarii oraz przestojów w produkcji.
Jakie są koszty zakupu i eksploatacji destylatora przemysłowego
Koszty zakupu i eksploatacji destylatora przemysłowego mogą się znacznie różnić w zależności od jego typu, wielkości oraz zastosowania. Inwestycja w nowoczesny destylator kolumnowy może wynosić od kilku tysięcy do nawet kilkuset tysięcy złotych, co sprawia, że jest to znaczący wydatek dla wielu przedsiębiorstw. Koszty te obejmują nie tylko samą cenę urządzenia, ale także dodatkowe elementy takie jak instalacja, szkolenie personelu oraz ewentualne modyfikacje infrastruktury zakładu. Po zakupie należy również uwzględnić koszty eksploatacji, które obejmują zużycie energii elektrycznej lub paliwa potrzebnego do podgrzewania cieczy, a także koszty konserwacji i serwisowania urządzenia. Warto również pamiętać o kosztach związanych z surowcami wykorzystywanymi w procesie destylacji oraz ewentualnymi kosztami związanymi z utylizacją odpadów.
Jakie są innowacje technologiczne w dziedzinie destylacji przemysłowej
W ostatnich latach dziedzina destylacji przemysłowej przechodzi dynamiczne zmiany dzięki wprowadzaniu innowacyjnych technologii. Jednym z najważniejszych trendów jest rozwój systemów automatyzacji i cyfryzacji procesów produkcyjnych. Dzięki zastosowaniu zaawansowanych algorytmów oraz sztucznej inteligencji możliwe jest optymalizowanie parametrów pracy destylatorów w czasie rzeczywistym, co przekłada się na zwiększenie wydajności oraz jakości produktów. Kolejnym istotnym kierunkiem rozwoju są technologie związane z odzyskiem energii oraz minimalizacją strat surowców. Nowoczesne systemy pozwalają na wykorzystanie ciepła odpadowego do podgrzewania innych procesów produkcyjnych, co znacząco obniża koszty operacyjne. Warto również zwrócić uwagę na rozwój materiałów konstrukcyjnych stosowanych w budowie destylatorów, które charakteryzują się większą odpornością na korozję oraz wysoką temperaturę, co zwiększa trwałość urządzeń.
Jakie są wymagania prawne dotyczące użytkowania destylatorów przemysłowych
Użytkowanie destylatorów przemysłowych wiąże się z koniecznością przestrzegania szeregu wymagań prawnych i norm regulujących działalność przemysłową. W Polsce przepisy te obejmują zarówno kwestie dotyczące bezpieczeństwa pracy, jak i ochrony środowiska. Przed rozpoczęciem działalności związanej z destylacją konieczne jest uzyskanie odpowiednich zezwoleń oraz spełnienie norm dotyczących emisji substancji szkodliwych do atmosfery oraz odpadów produkcyjnych. Wiele branż objętych jest dodatkowymi regulacjami dotyczącymi jakości produktów końcowych, co ma szczególne znaczenie w przypadku przemysłu spożywczego czy farmaceutycznego. Pracownicy obsługujący destylatory muszą być odpowiednio przeszkoleni i posiadać wiedzę na temat zasad BHP oraz obsługi urządzeń. Regularne kontrole stanu technicznego sprzętu oraz przestrzeganie procedur konserwacyjnych są kluczowe dla zapewnienia bezpieczeństwa pracy oraz zgodności z obowiązującymi przepisami prawnymi.
Jakie są perspektywy rozwoju rynku destylatorów przemysłowych
Perspektywy rozwoju rynku destylatorów przemysłowych wyglądają obiecująco, zwłaszcza w kontekście rosnącego zapotrzebowania na czyste źródła energii oraz produkty o wysokiej jakości. Zwiększone zainteresowanie ekologicznymi rozwiązaniami sprawia, że wiele firm inwestuje w nowoczesne technologie destylacyjne, które pozwalają na efektywne wykorzystanie surowców oraz minimalizację negatywnego wpływu na środowisko. W miarę jak rośnie świadomość ekologiczna społeczeństwa oraz regulacje dotyczące ochrony środowiska stają się coraz bardziej rygorystyczne, przedsiębiorstwa będą musiały dostosować swoje procesy produkcyjne do nowych standardów. Dodatkowo rozwój sektora biotechnologii oraz farmaceutyki stwarza nowe możliwości dla producentów destylatorów, którzy mogą oferować specjalistyczne rozwiązania dostosowane do specyfiki tych branż. Również wzrost globalnej populacji i zapotrzebowania na żywność przyczyniają się do rozwoju technologii związanych z produkcją alkoholu oraz ekstraktów roślinnych.
Jakie są najlepsze praktyki dotyczące obsługi destylatorów przemysłowych
Aby zapewnić prawidłowe działanie i długowieczność destylatora przemysłowego, warto wdrożyć najlepsze praktyki dotyczące jego obsługi i konserwacji. Kluczowym aspektem jest regularne przeprowadzanie przeglądów technicznych oraz konserwacji urządzenia zgodnie z zaleceniami producenta. Należy również monitorować parametry pracy destylatora, takie jak temperatura czy ciśnienie, aby szybko reagować na ewentualne nieprawidłowości. Szkolenie personelu obsługującego urządzenie jest równie istotne – pracownicy powinni być dobrze zaznajomieni z zasadami BHP oraz procedurami awaryjnymi. Odpowiednie zarządzanie surowcami wykorzystywanymi w procesie destylacji również ma kluczowe znaczenie; należy dbać o ich jakość oraz czystość, aby uniknąć osadzenia się zanieczyszczeń w kolumnach frakcyjnych. Ważne jest także prowadzenie dokumentacji dotyczącej wszystkich operacji przeprowadzanych na urządzeniu, co pozwala na lepsze zarządzanie procesem produkcyjnym oraz identyfikację potencjalnych problemów.