Łączenie dwóch kompresorów to proces, który może przynieść wiele korzyści, zwłaszcza w kontekście zwiększenia wydajności i efektywności systemu pneumatycznego. Warto zacząć od zrozumienia, jakie są różnice między różnymi typami kompresorów oraz jakie mają one zastosowanie. Kompresory tłokowe, śrubowe czy membranowe różnią się nie tylko konstrukcją, ale także sposobem pracy i wydajnością. Przy łączeniu dwóch kompresorów kluczowe jest, aby były one kompatybilne pod względem technicznym i wydajnościowym. Należy również zwrócić uwagę na ich parametry, takie jak ciśnienie robocze oraz przepływ powietrza. W praktyce można zastosować różne metody łączenia, takie jak równoległe lub szeregowe połączenie kompresorów. Równoległe połączenie pozwala na zwiększenie wydajności, podczas gdy szeregowe może być korzystne w przypadku potrzeby uzyskania wyższego ciśnienia.
Jakie narzędzia są potrzebne do połączenia kompresorów?
Aby skutecznie połączyć dwa kompresory, niezbędne jest posiadanie odpowiednich narzędzi oraz materiałów. Podstawowym narzędziem będzie klucz do rur oraz zestaw kluczy nasadowych, które umożliwią dokręcenie wszystkich połączeń. Warto również zaopatrzyć się w wkrętarkę elektryczną lub ręczną, co znacznie przyspieszy proces montażu. Oprócz narzędzi mechanicznych istotne będą także elementy instalacyjne, takie jak rury pneumatyczne o odpowiedniej średnicy oraz złączki do ich łączenia. W przypadku połączeń równoległych konieczne będą także zawory kulowe oraz manometry do monitorowania ciśnienia w systemie. Dobrze jest mieć pod ręką uszczelki oraz taśmy teflonowe, które zapewnią szczelność połączeń i zapobiegną wyciekom powietrza. Przed przystąpieniem do pracy warto przygotować plan działania oraz schemat instalacji, co ułatwi cały proces i pozwoli uniknąć błędów.
Jakie są zalety łączenia dwóch kompresorów?
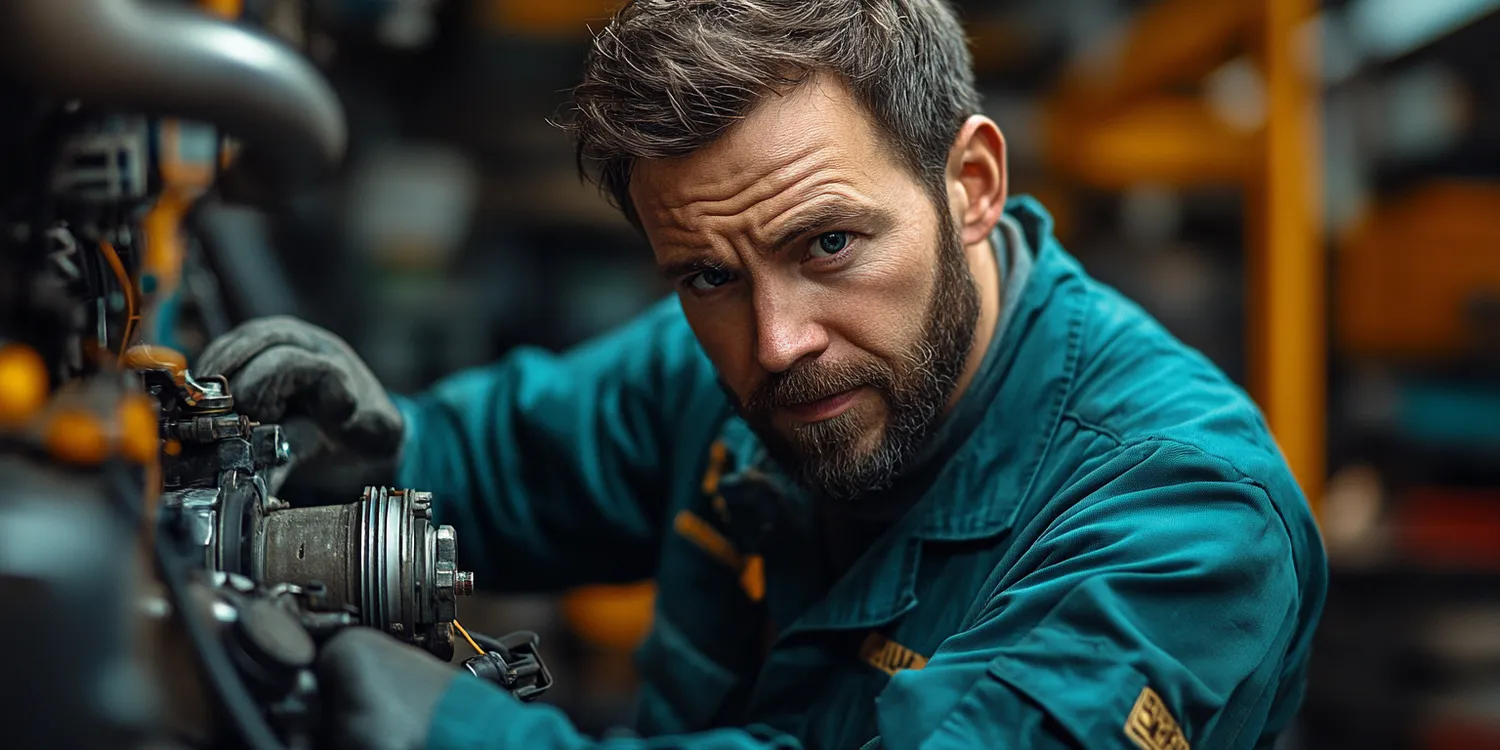
Jak połączyć dwa kompresory?
Łączenie dwóch kompresorów niesie ze sobą wiele korzyści, które mogą znacząco wpłynąć na efektywność pracy systemu pneumatycznego. Przede wszystkim zwiększa to ogólną wydajność całego układu, co jest szczególnie istotne w przemysłowych zastosowaniach wymagających dużych ilości sprężonego powietrza. Dzięki równoległemu połączeniu kompresorów możliwe jest osiągnięcie większego przepływu powietrza bez konieczności inwestowania w droższe modele o wyższej wydajności. Kolejną zaletą jest możliwość redundancji – w przypadku awarii jednego z urządzeń drugie może przejąć jego funkcje, co zapewnia ciągłość pracy i minimalizuje przestoje. Łączenie kompresorów pozwala również na lepsze zarządzanie energią elektryczną – można dostosować pracę urządzeń do aktualnych potrzeb produkcyjnych, co przekłada się na oszczędności finansowe. Warto także wspomnieć o możliwości łatwiejszej konserwacji i serwisowania systemu, ponieważ można rozdzielić obciążenia między dwa urządzenia.
Jakie problemy mogą wystąpić przy łączeniu kompresorów?
Podczas łączenia dwóch kompresorów mogą wystąpić różnorodne problemy techniczne oraz operacyjne, które warto mieć na uwadze przed przystąpieniem do montażu. Jednym z najczęstszych problemów jest niewłaściwe dopasowanie parametrów obu urządzeń – różnice w ciśnieniu roboczym czy wydajności mogą prowadzić do nieefektywnej pracy całego systemu. W przypadku równoległego połączenia jeden z kompresorów może pracować intensywniej niż drugi, co prowadzi do szybszego zużycia jego komponentów i potencjalnych awarii. Innym istotnym zagadnieniem są kwestie związane z instalacją – niewłaściwe wykonanie połączeń lub użycie nieodpowiednich materiałów może skutkować wyciekami powietrza lub nawet uszkodzeniem sprzętu. Dodatkowo należy pamiętać o konieczności regularnego serwisowania obu urządzeń oraz monitorowania ich stanu technicznego, aby uniknąć niespodziewanych awarii w trakcie pracy.
Jakie są najlepsze metody łączenia kompresorów?
Wybór odpowiedniej metody łączenia kompresorów jest kluczowy dla osiągnięcia zamierzonych efektów w zakresie wydajności i efektywności systemu pneumatycznego. Istnieją dwie główne metody, które można zastosować: połączenie równoległe oraz szeregowe. Połączenie równoległe polega na tym, że oba kompresory pracują jednocześnie, co pozwala na zwiększenie całkowitego przepływu powietrza. Tego typu rozwiązanie jest szczególnie korzystne w sytuacjach, gdy wymagane są duże ilości sprężonego powietrza, na przykład w zakładach przemysłowych czy warsztatach. W przypadku połączenia szeregowego jeden kompresor działa jako wsparcie dla drugiego, co pozwala na uzyskanie wyższego ciśnienia. Tego rodzaju układ może być przydatny w aplikacjach wymagających dużego ciśnienia roboczego, takich jak niektóre procesy technologiczne czy urządzenia pneumatyczne. Niezależnie od wybranej metody, kluczowe jest zapewnienie odpowiednich warunków pracy dla obu urządzeń oraz ich właściwej konserwacji.
Jakie są koszty związane z łączeniem kompresorów?
Decyzja o połączeniu dwóch kompresorów wiąże się z różnymi kosztami, które warto dokładnie przeanalizować przed podjęciem ostatecznej decyzji. Pierwszym aspektem są koszty zakupu dodatkowego sprzętu i materiałów potrzebnych do instalacji. Może to obejmować rury pneumatyczne, złączki, zawory oraz manometry, które są niezbędne do prawidłowego funkcjonowania systemu. Koszty te mogą się znacznie różnić w zależności od wybranych materiałów oraz skali projektu. Kolejnym istotnym elementem są koszty robocizny związane z montażem i uruchomieniem układu. Jeśli zdecydujemy się na zatrudnienie specjalistycznej firmy do wykonania tych prac, należy uwzględnić dodatkowe wydatki na usługi fachowców. Nie można również zapominać o przyszłych kosztach eksploatacji – łączenie kompresorów może wpłynąć na zużycie energii elektrycznej oraz wymogi dotyczące konserwacji urządzeń. Warto także rozważyć potencjalne oszczędności wynikające z większej wydajności systemu oraz mniejszych przestojów spowodowanych awariami.
Jakie są najczęstsze błędy przy łączeniu kompresorów?
Podczas łączenia dwóch kompresorów istnieje wiele pułapek, które mogą prowadzić do problemów technicznych oraz operacyjnych. Jednym z najczęstszych błędów jest niewłaściwe dopasowanie parametrów obu urządzeń. Różnice w ciśnieniu roboczym lub wydajności mogą prowadzić do nieefektywnej pracy całego systemu, a nawet uszkodzenia jednego z kompresorów. Innym powszechnym błędem jest niewłaściwe wykonanie połączeń instalacyjnych – źle dobrane rury czy złączki mogą skutkować wyciekami powietrza oraz obniżeniem ogólnej wydajności systemu. Często zdarza się także ignorowanie konieczności monitorowania stanu technicznego obu urządzeń oraz ich regularnej konserwacji. Brak odpowiedniej dbałości o sprzęt może prowadzić do szybszego zużycia komponentów i częstszych awarii. Ważne jest również, aby nie pomijać kwestii bezpieczeństwa – niewłaściwie zaprojektowany układ może stwarzać zagrożenie dla użytkowników oraz otoczenia.
Jakie są zasady bezpieczeństwa przy łączeniu kompresorów?
Bezpieczeństwo podczas łączenia dwóch kompresorów powinno być priorytetem na każdym etapie tego procesu. Przede wszystkim należy przestrzegać zasad dotyczących obsługi urządzeń pneumatycznych oraz stosować się do zaleceń producenta dotyczących instalacji i eksploatacji sprzętu. Kluczowe jest również zapewnienie odpowiednich warunków pracy – miejsce montażu powinno być dobrze wentylowane, a dostęp do urządzeń powinien być swobodny, aby umożliwić łatwą konserwację i serwisowanie. Warto również zwrócić uwagę na użycie odpowiednich środków ochrony osobistej podczas pracy z narzędziami i materiałami instalacyjnymi – rękawice ochronne, okulary czy kaski mogą znacząco zmniejszyć ryzyko urazów. Należy także pamiętać o regularnym sprawdzaniu stanu technicznego zarówno kompresorów, jak i elementów instalacyjnych – wszelkie uszkodzenia powinny być natychmiast naprawiane, aby uniknąć potencjalnych zagrożeń związanych z wyciekami powietrza czy innymi awariami.
Jakie są alternatywy dla łączenia dwóch kompresorów?
Łączenie dwóch kompresorów to tylko jedna z wielu opcji dostępnych dla osób poszukujących sposobu na zwiększenie wydajności systemu pneumatycznego. Istnieją również inne rozwiązania, które mogą okazać się równie skuteczne lub nawet bardziej efektywne w określonych warunkach. Jedną z alternatyw jest inwestycja w jeden większy kompresor o wyższej wydajności, który będzie w stanie sprostać wymaganiom produkcyjnym bez potrzeby łączenia dwóch jednostek. Takie podejście może uprościć instalację oraz zmniejszyć ryzyko wystąpienia problemów związanych z kompatybilnością różnych modeli urządzeń. Inną możliwością jest zastosowanie akumulatora powietrznego, który gromadzi sprężone powietrze i uwalnia je w razie potrzeby, co pozwala na optymalizację pracy pojedynczego kompresora bez konieczności jego ciągłego działania na pełnej mocy.
Jakie są opinie użytkowników na temat łączenia kompresorów?
Opinie użytkowników dotyczące łączenia dwóch kompresorów są bardzo zróżnicowane i często zależą od indywidualnych doświadczeń oraz specyfiki zastosowań danego systemu pneumatycznego. Wielu użytkowników podkreśla korzyści płynące z równoległego połączenia kompresorów, takie jak zwiększona wydajność oraz możliwość elastycznego dostosowywania pracy urządzeń do aktualnych potrzeb produkcyjnych. Użytkownicy często zauważają również zalety redundancji – możliwość kontynuowania pracy nawet w przypadku awarii jednego z urządzeń jest dla nich kluczowym atutem tego rozwiązania. Z drugiej strony pojawiają się także głosy krytyki dotyczące komplikacji związanych z instalacją oraz konieczności regularnego serwisowania obu jednostek. Niektórzy użytkownicy wskazują na problemy związane z różnicami w parametrach technicznych poszczególnych kompresorów, co może prowadzić do nieefektywnej pracy całego systemu.